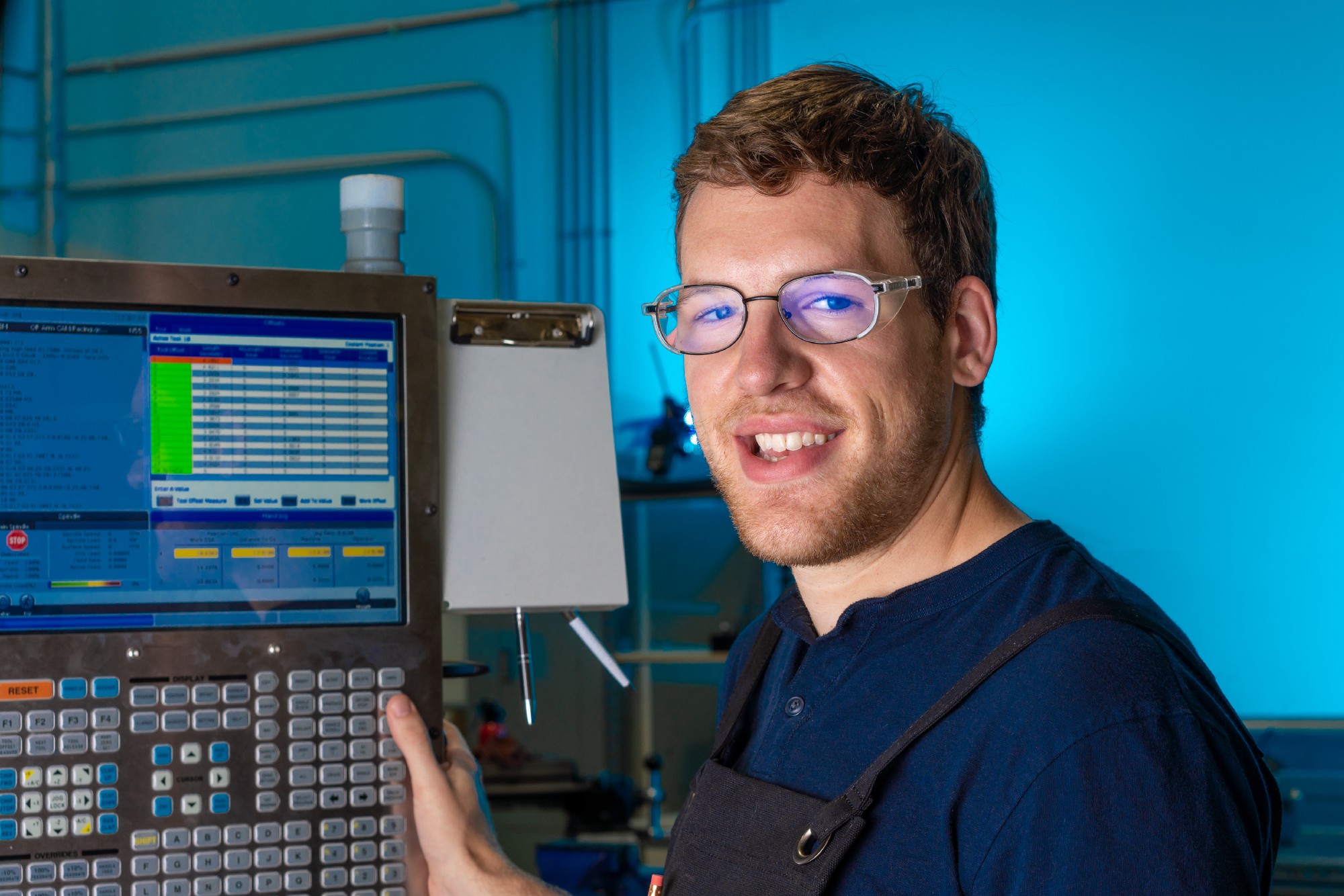
The unassuming (but essential) things you need to run a safe and efficient prototyping shop
While setting up a prototyping space for developing physical products, the main focus is usually on selecting the machines. Rightly so; they’re often pricey and critical in getting you up and running fast. Through years of running Bolt’s prototyping shops in Boston and San Francisco, we’ve noticed that machines and hand tools are only a fraction of the challenge. If your space is used by lots of people with a variety of goals, like ours are, there are many other items that you need to support them and their workspace.
Any extra time spent looking for safety gear or a tool is a detriment to making progress.
In short: the boring stuff. We’re excited to recommend some things that you may not think about until after the fun toys have arrived. It’s important to keep in mind that our main goal in the shop is to allow our users to build early versions of their product, test them, feed the results back into design changes, and repeat. They must be able to iterate as fast as possible, so the main purpose of the infrastructure and tools is to enable them to move quickly and efficiently while staying safe. Any extra time spent looking for safety gear or a tool is a detriment to making progress.
Marking
Marking things is critical for keeping tools organized and making life easier. A marked tool is less likely to leave the shop and, if it does, it’s more likely to find its way back home. You’ll never have a need for the dreaded bin of “unsorted fasteners” if you have enough bins to mark with a fastener type (I’m of the opinion that a bin like that should never exist, but that’s an argument for another day). If the tools are made available to all, users will start marking things themselves before you know it.
Easily the most critical item to have in this category is a label maker. It doesn’t really matter which you get, as long as you have at least one, but we like ours. Make sure to keep an extra roll of labels on hand at all times.
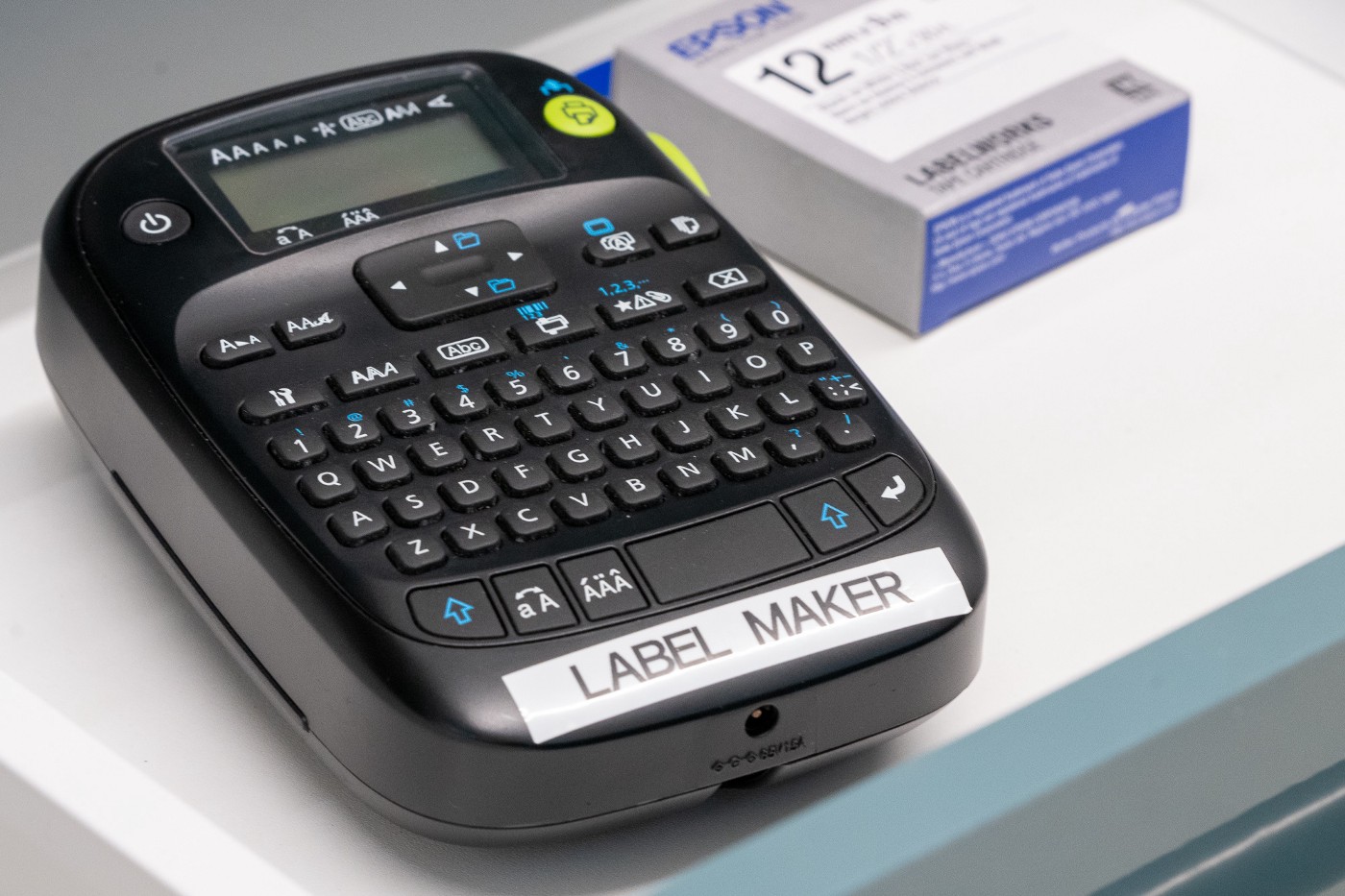
Sadly, these don’t work well for marking tools with rounded surfaces such as allen keys or screwdrivers. For this, we like using heatshrink tubing. Pick up a variety of sizes in a color that indicates the owner (in our shops, Bolt tools are marked in yellow), and get the adhesive-lined kind if you can. For bonus points, try branded heatshrink or pick up a heatshrink printer.
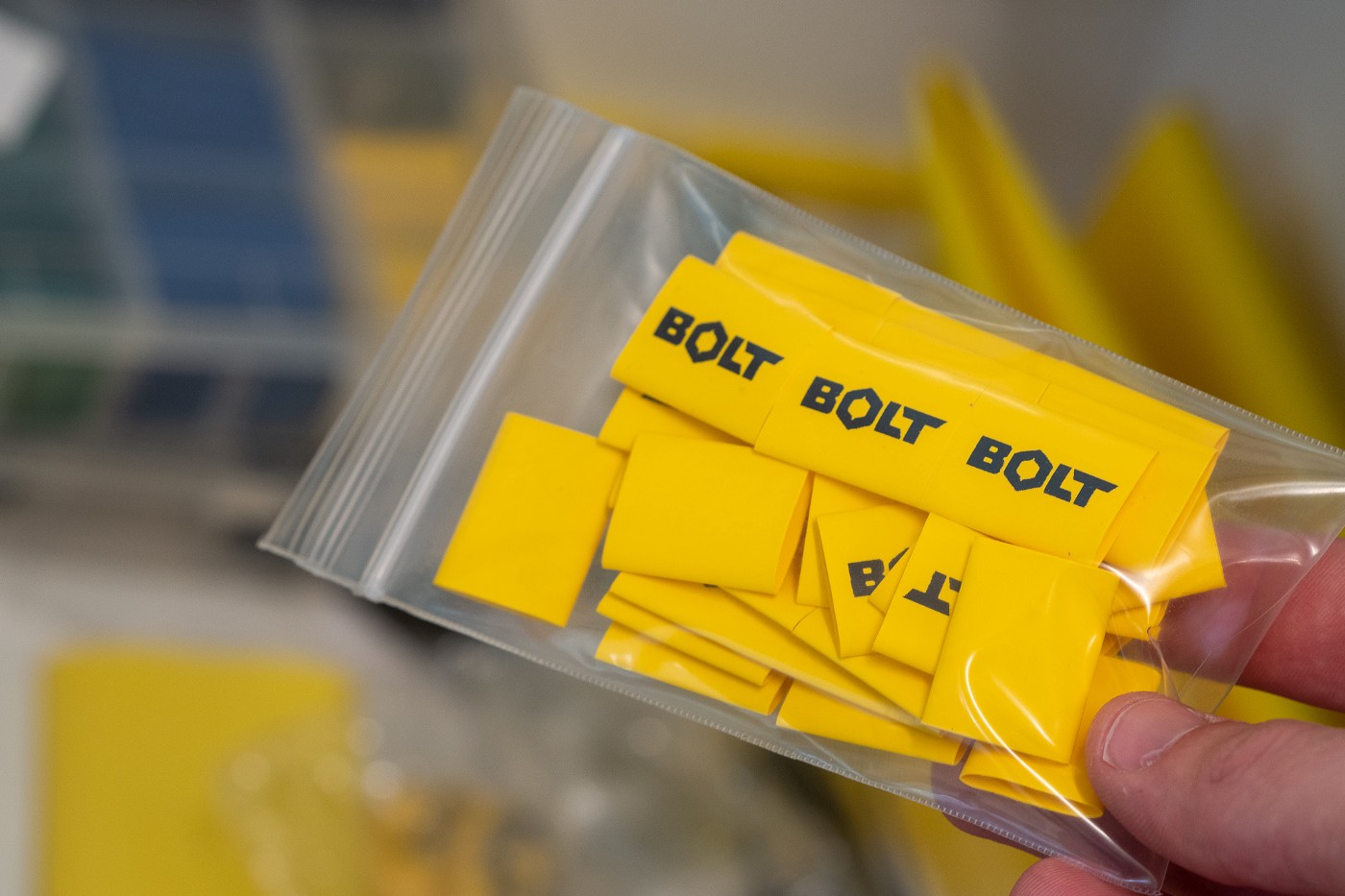
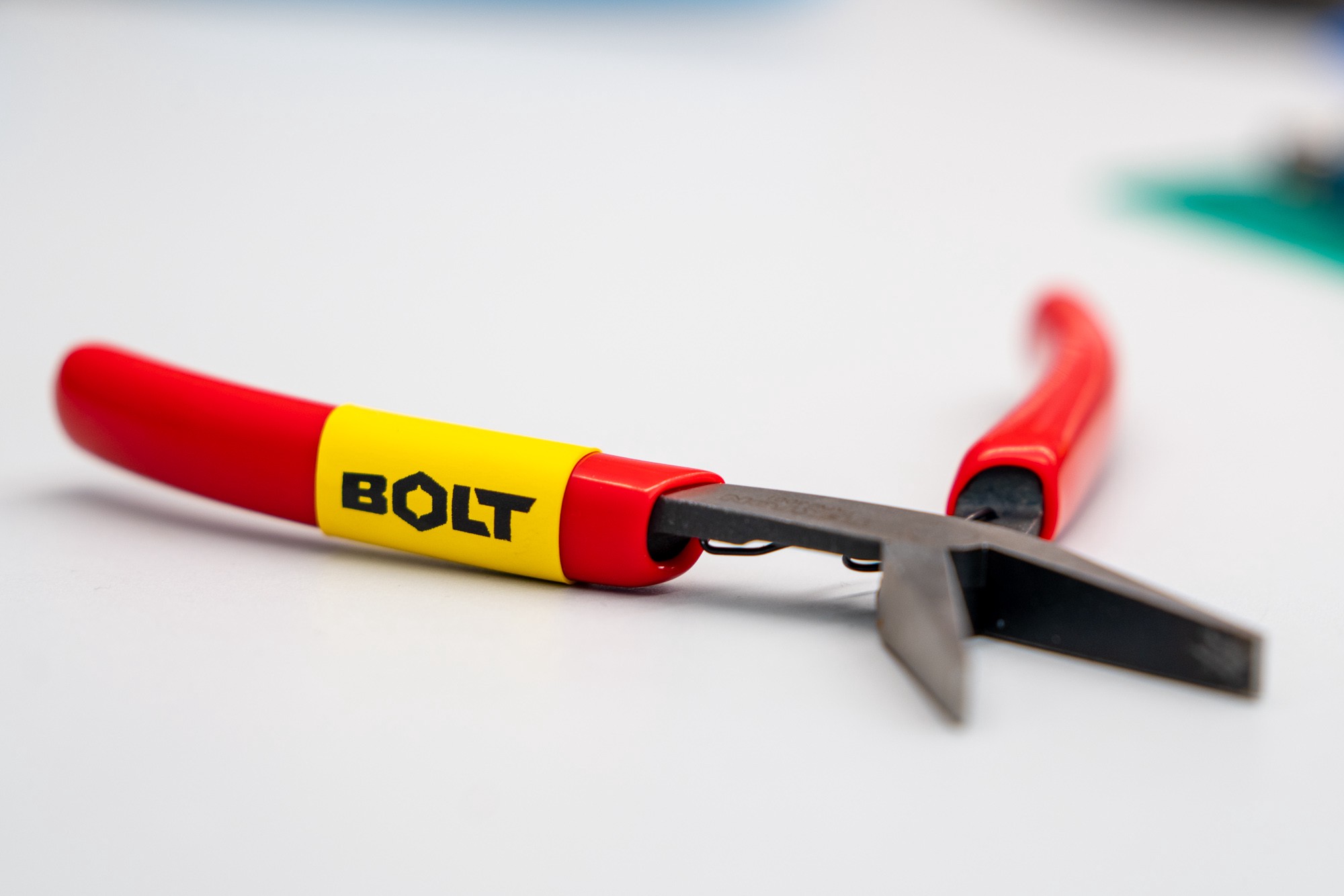
The most basic marking tools are absolutely critical to have around in bulk: painters tape (the original blue stuff works best) and sharpies (the twin-tip kind) are your friends. We buy these in large quantities every few months.
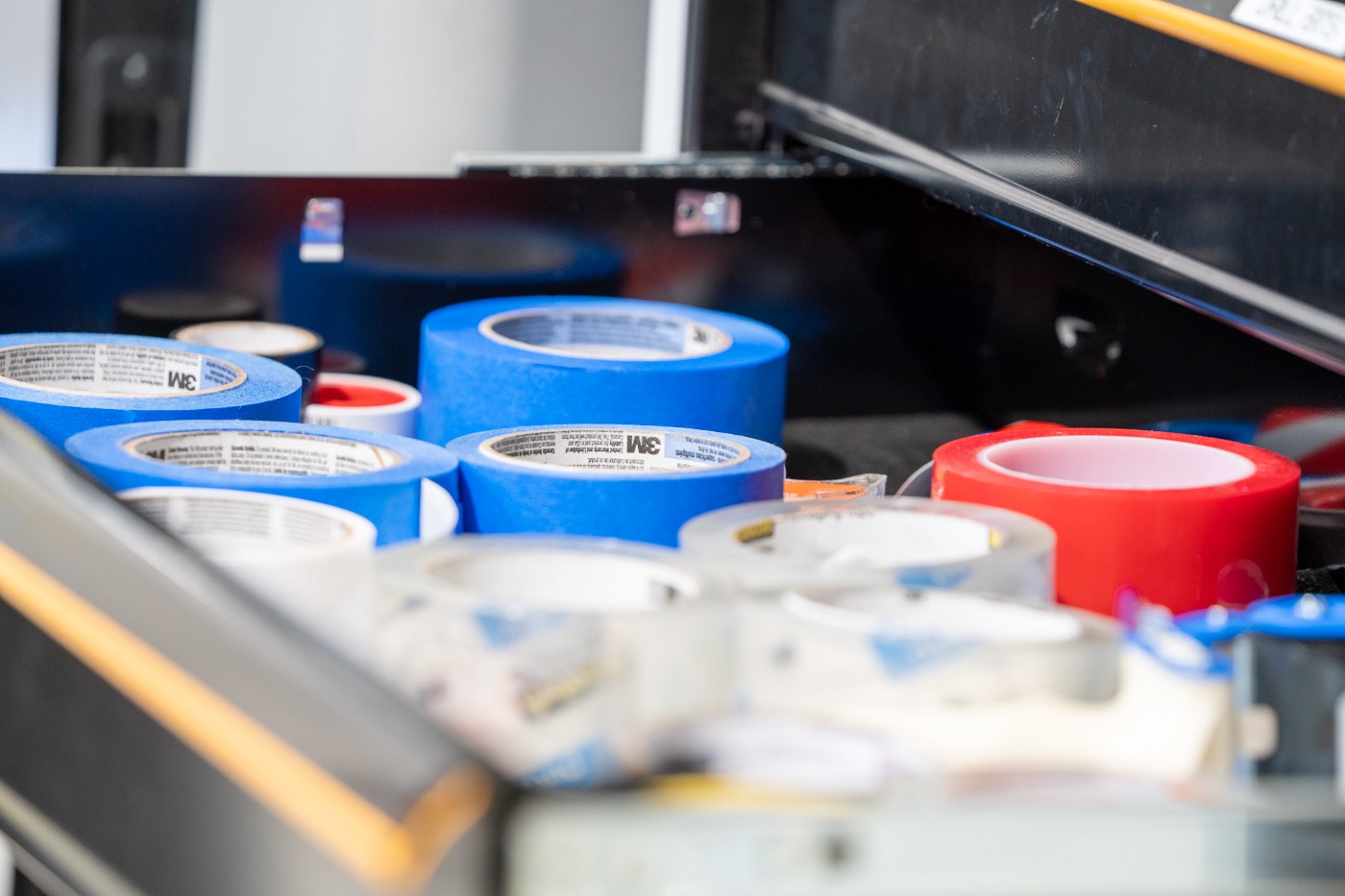
Whiteboards are great for asynchronous communication between shop users, as is dry erase tape. Instead of requiring that users email purchase suggestions to the shop manager, put up a small whiteboard. We assume that most users forget what they mentally added as a “to buy” item by the time they get back to their desk, so the whiteboard works great for noting things while they’re top-of-mind.
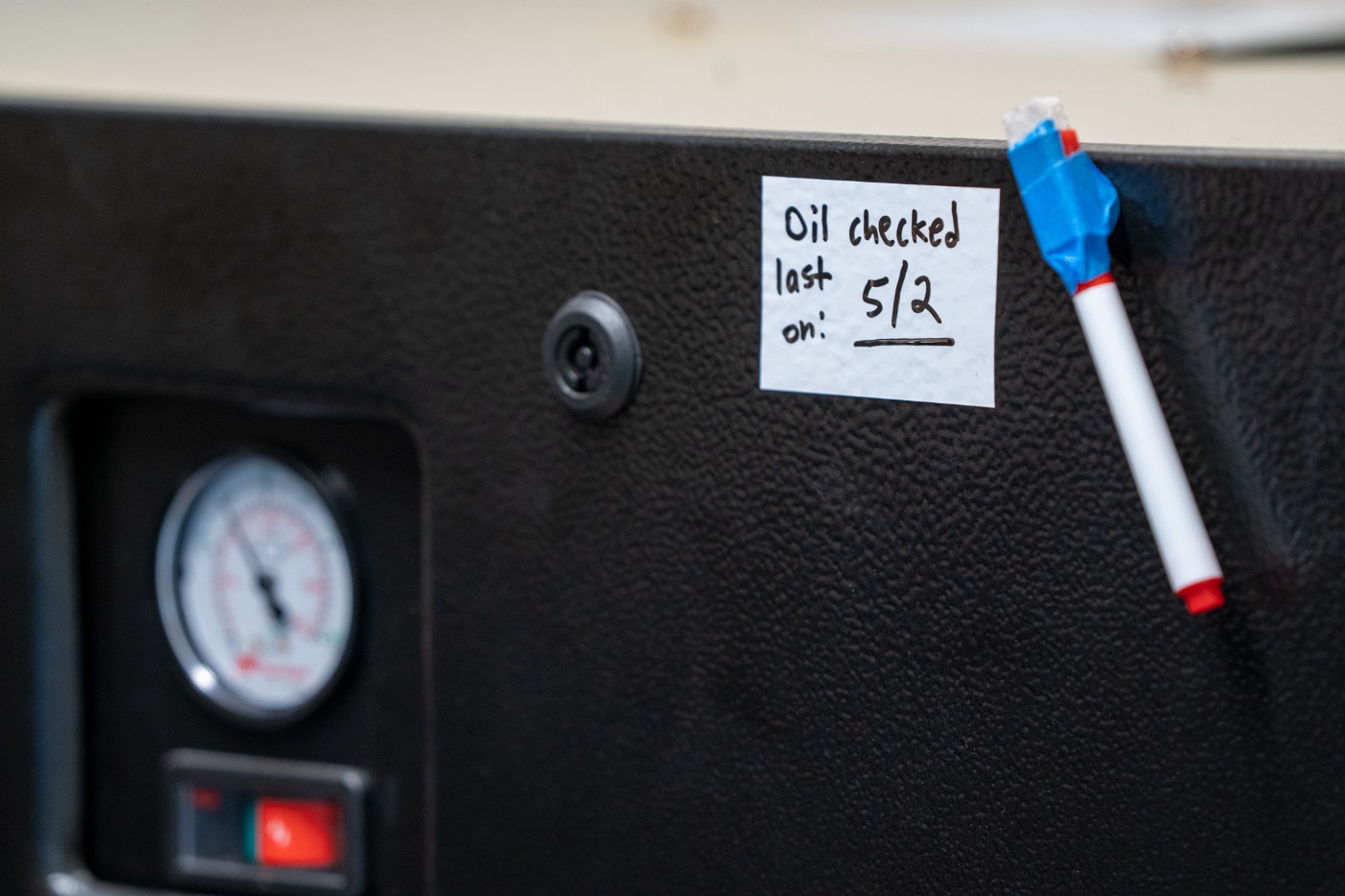
This is getting into machine territory, but vinyl cutters are an oft-avoided purchase that we recommend for marking. The Explore Air 2 from Cricut is great to have around for cutting custom machine markings, stickers, potential logos, or for prototyping parts that will eventually be die-cut. It won’t break the bank, although the web-based software experience leaves a bit to be desired (especially when moving files over from a CAD program). The natural upgrade from a Cricut is a more capable Roland machine, which adds the ability to cut very long lengths of vinyl.
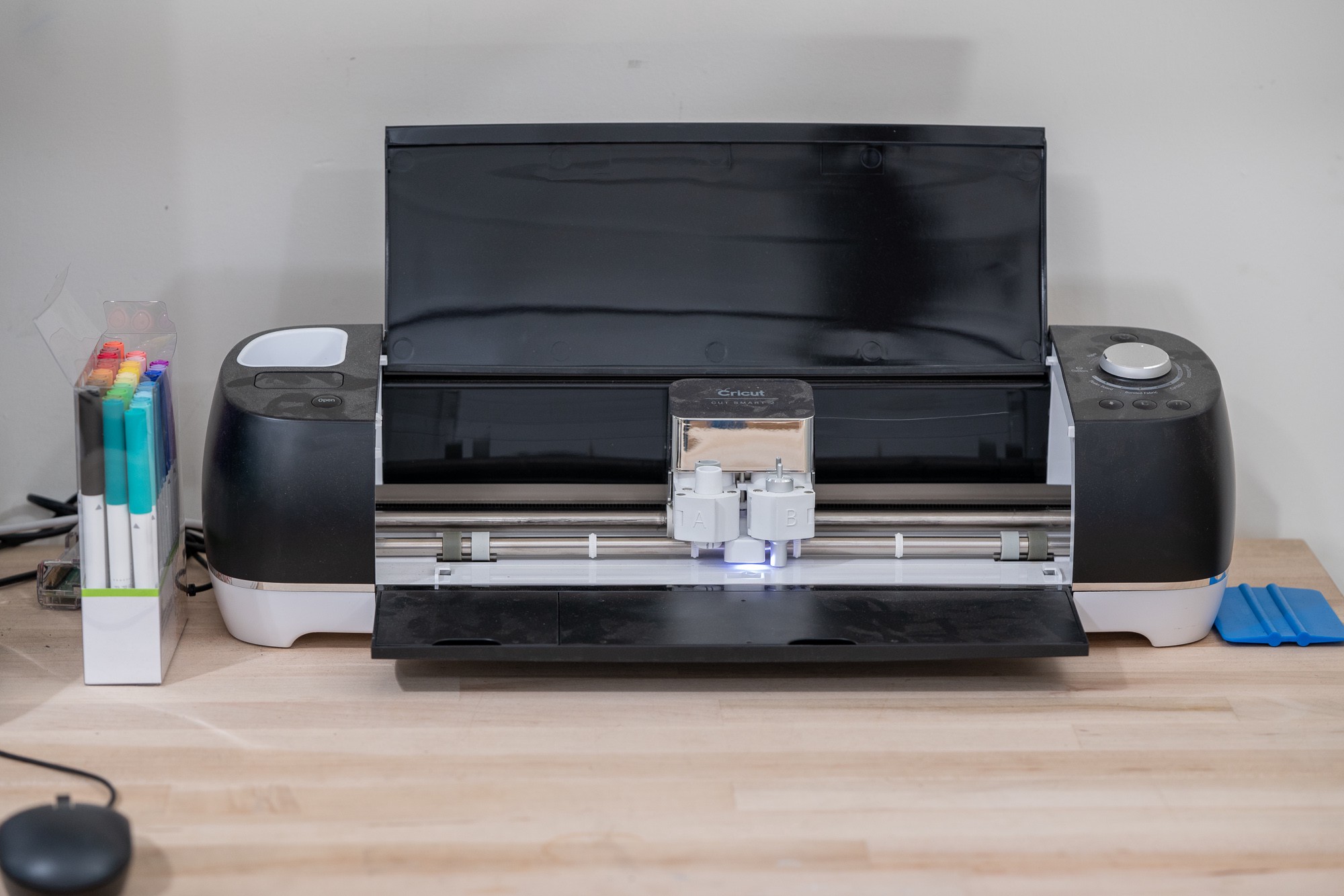
Organization
When you host teams that build hardware in a shared space, they will inevitably start storing inventory, spare parts and previous builds around their work area. The storage solution that pairs best with the painters and whiteboard tapes mentioned above are foldable cardboard bins. They’re cheap, are easy to store en-masse, come in a bunch of sizes, and are quick to fold.
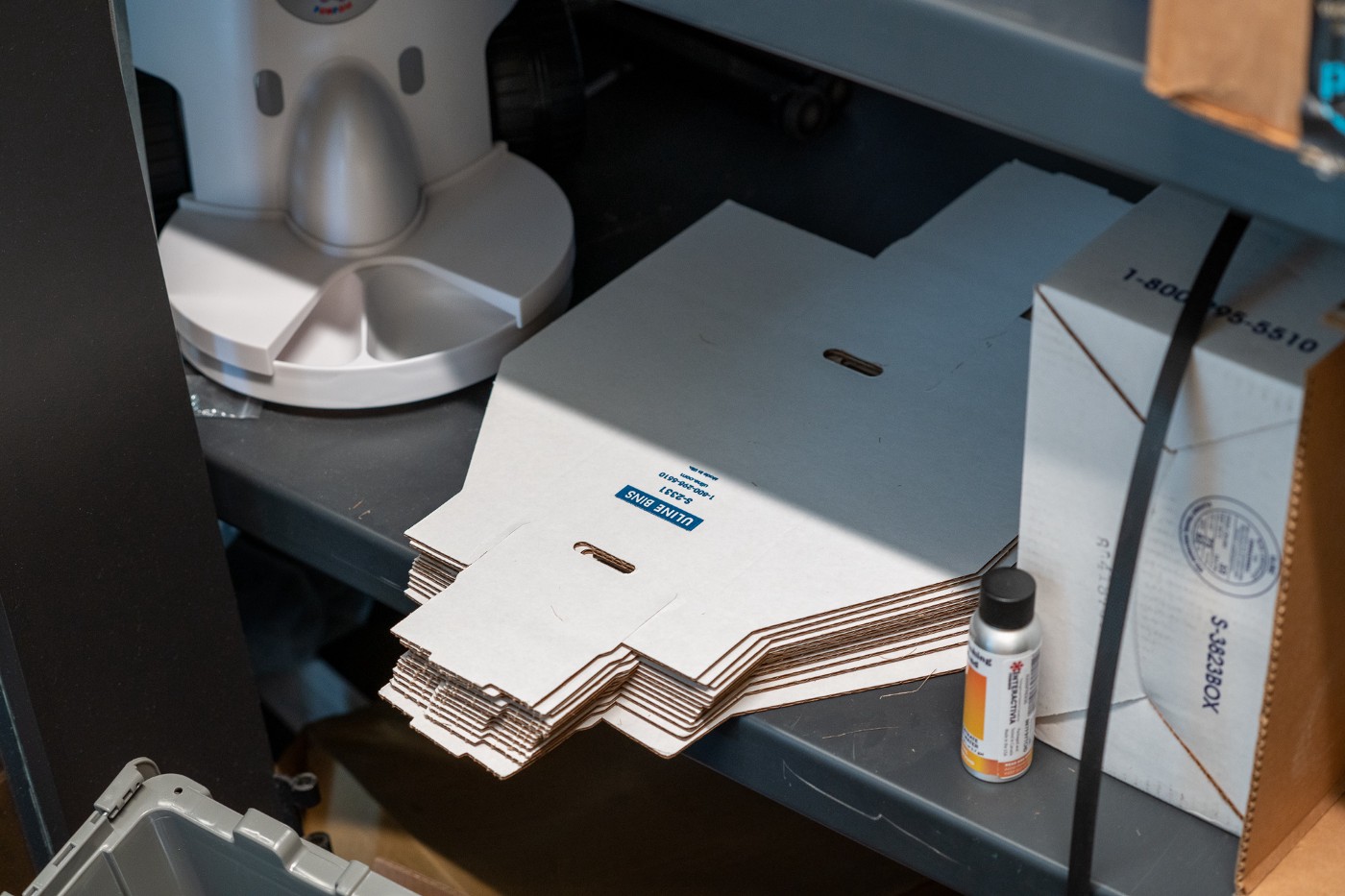
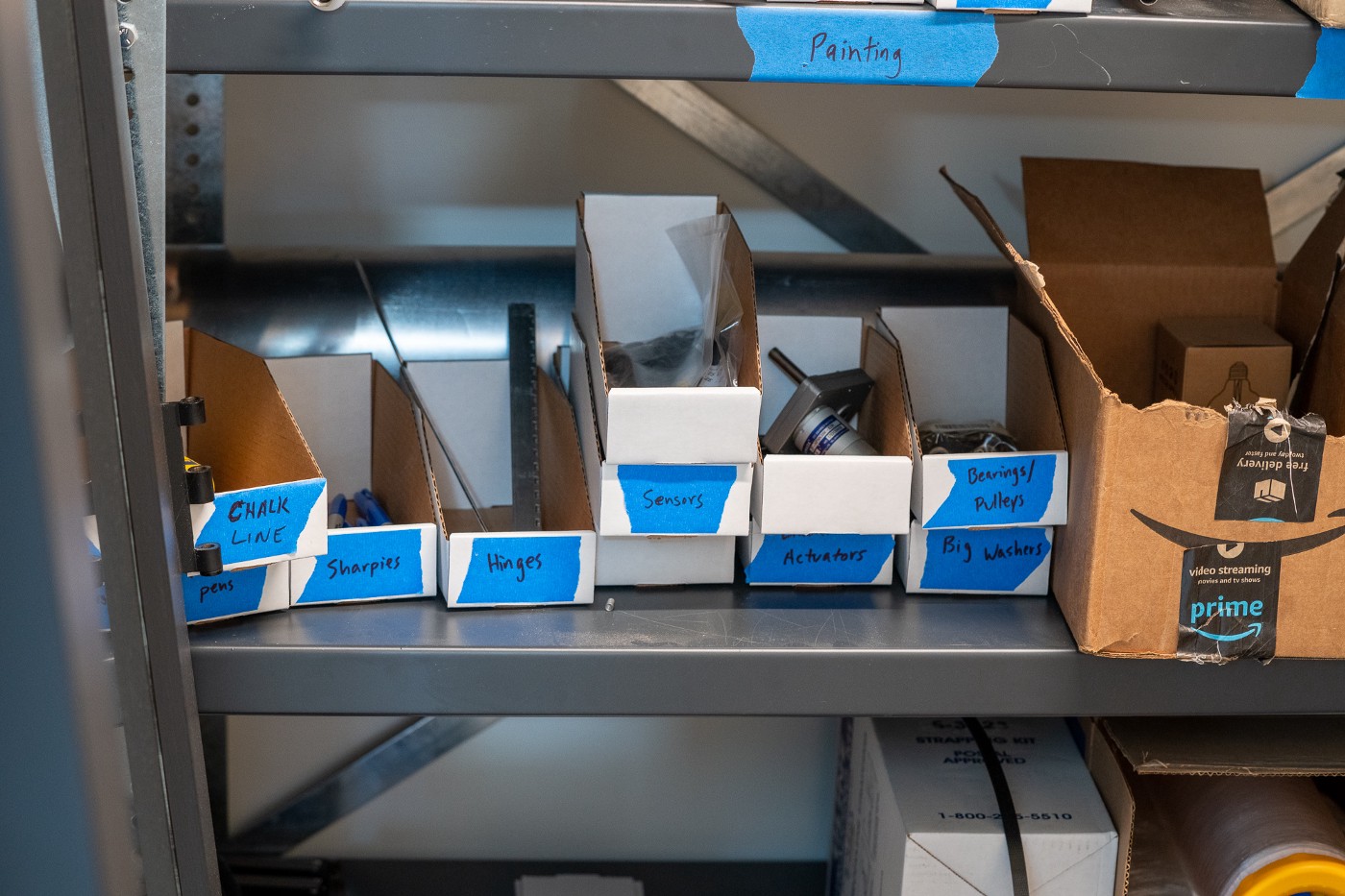
The typical upgrade from the foldable cardboard bins are plastic bins, also from Uline. They are rock solid but only useful for storing a few types of items, in our experience. They’re far more expensive than the cardboard ones and harder to store when not in use, but work well for holding fasteners and small parts that may slip under the cracks of the foldable bins. We stock a variety of commonly-used fasteners on a wall mount panel rack and consumables such as cable ties, cups and stirrers on a mobile workstation. The sloped inside surface of the plastic bins make it easy to pull parts out of them: ideal for tiny fasteners.
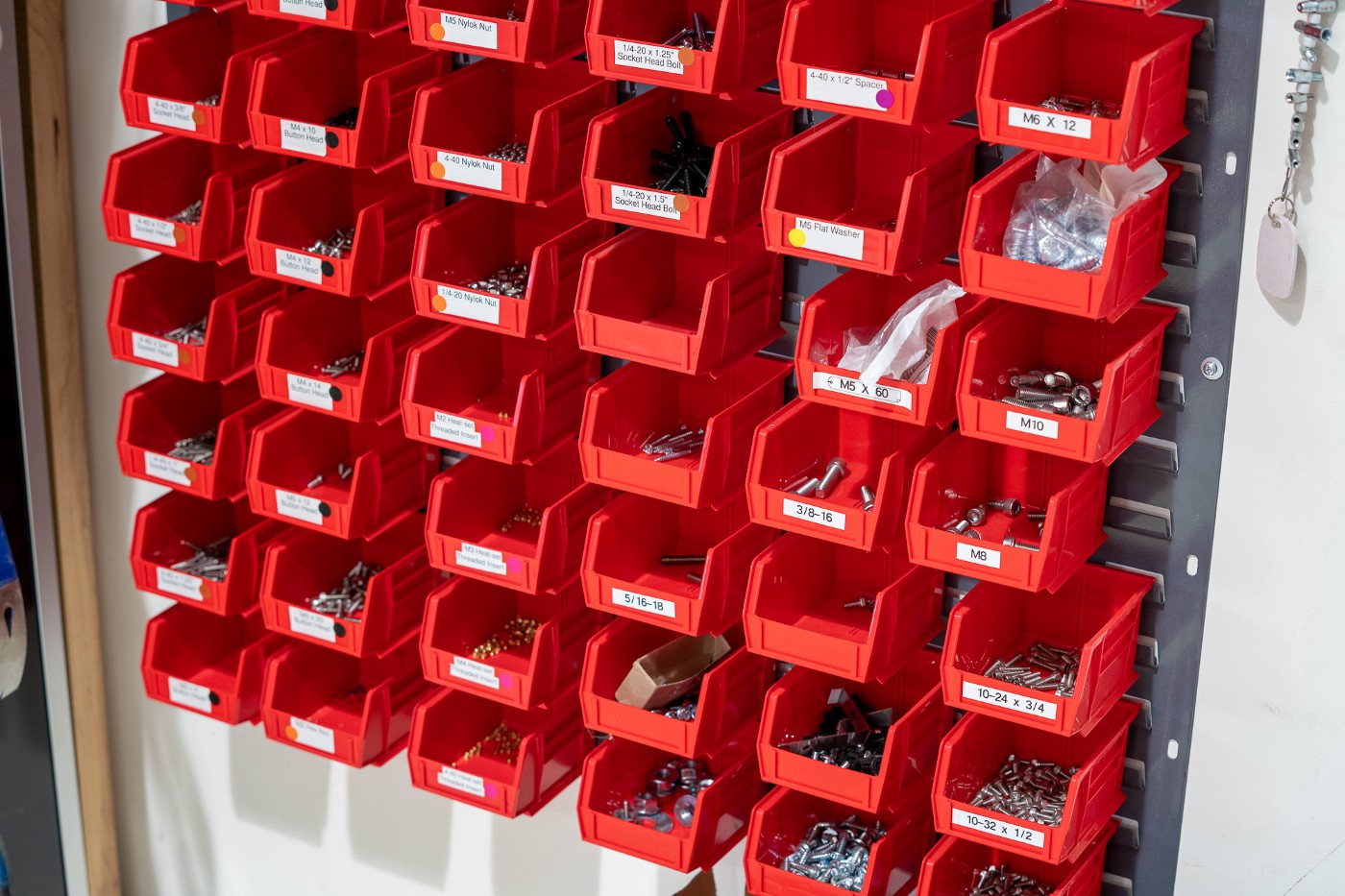

To mitigate the spread of inventory boxes into the walkways of your shop space, I highly recommend offering large storage containers for teams to take advantage of. These bins work well, and pair nicely with boltless shelves, which don’t require anything but a hammer to assemble.
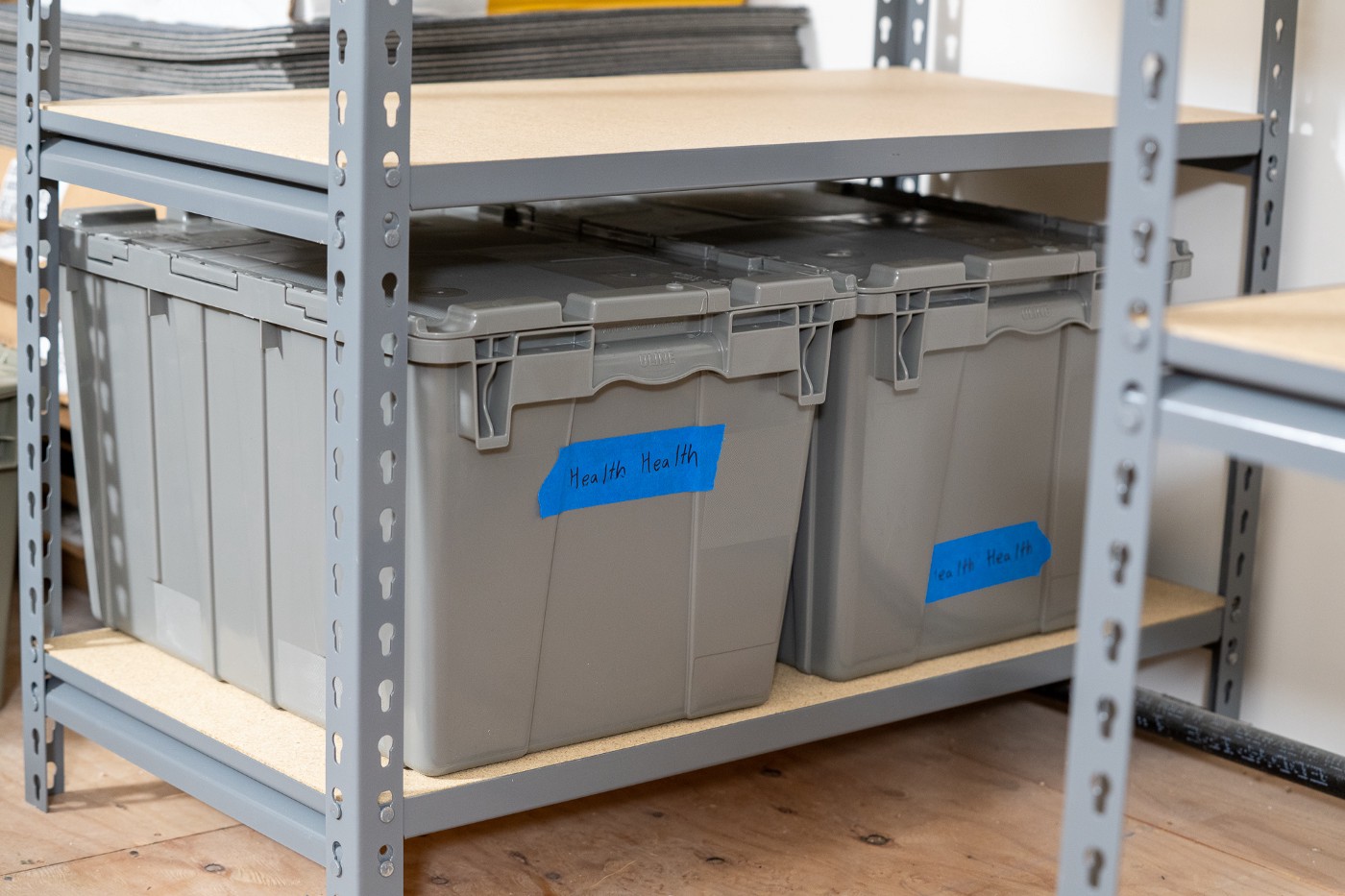
Our electronics lab is full of Ikea cabinets for tool storage, so Ikea’s kitchen utensil trays are ideal for splitting the drawers into sections.
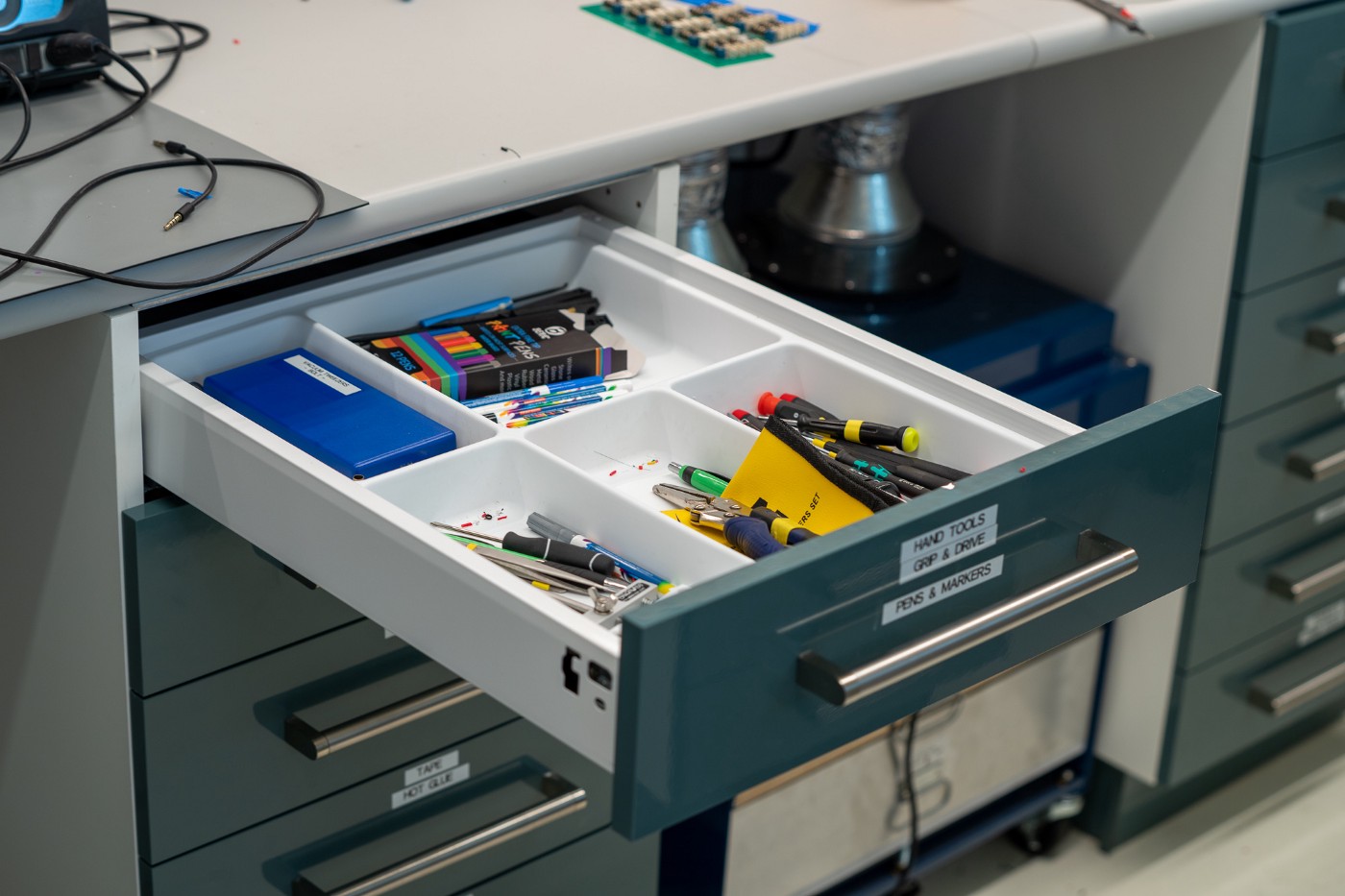
The lab is also full of benchtop devices that require power such as soldering irons, oscilloscopes and hot-air rework stations. Instead of routing the power cables for these into a wall outlet, we plug them right into a wall-mounted Tripp Lite power strip. They won’t break the bank, come in lengths up to 6′ and have plenty of outlets.
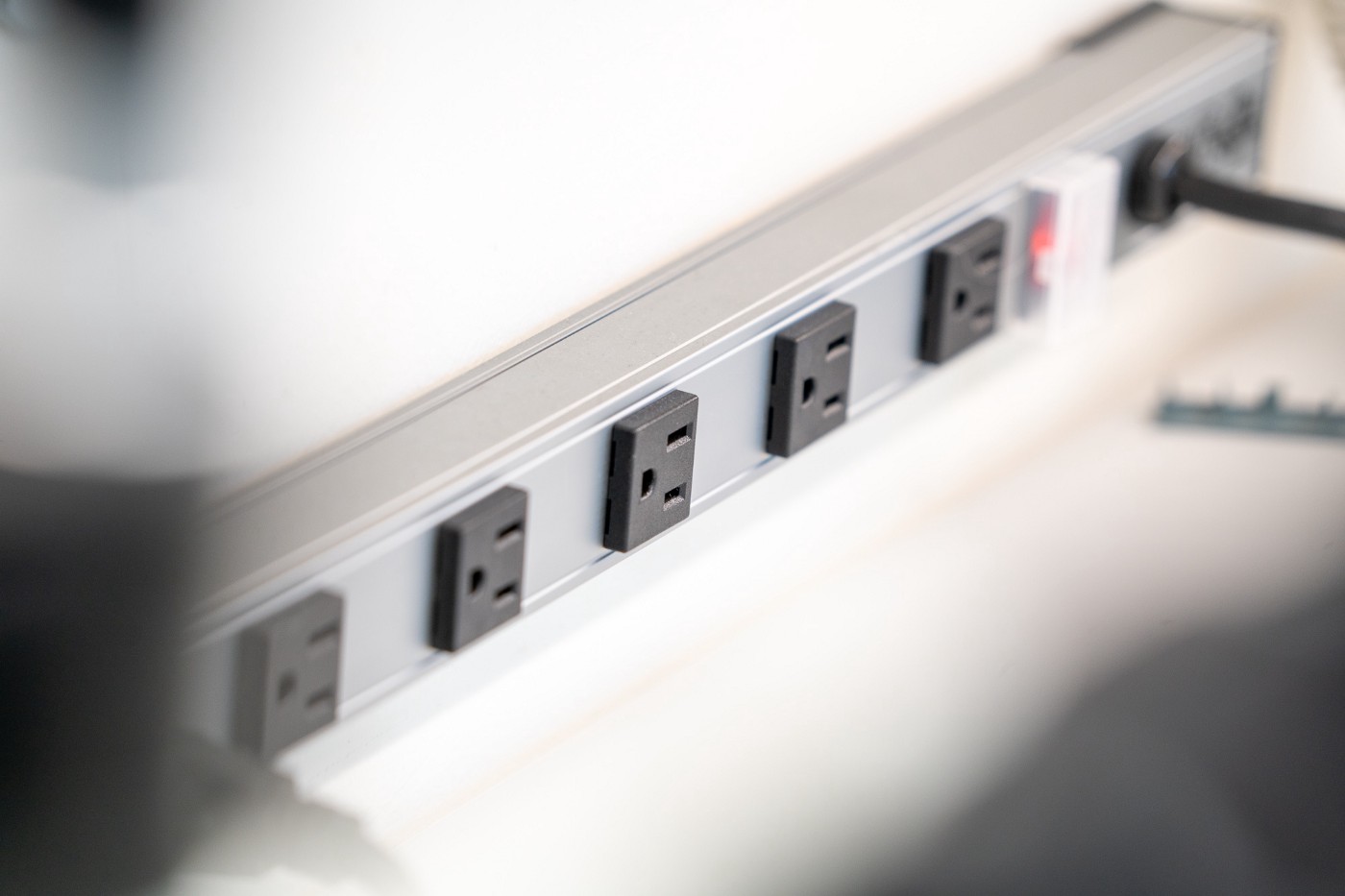
Our machining area is full of cutting inserts, endmills, nuts and threaded rod for fixturing, so keeping them separated with bins is helpful. We like these, by Schaller, which are affordable in bulk and nest nicely.
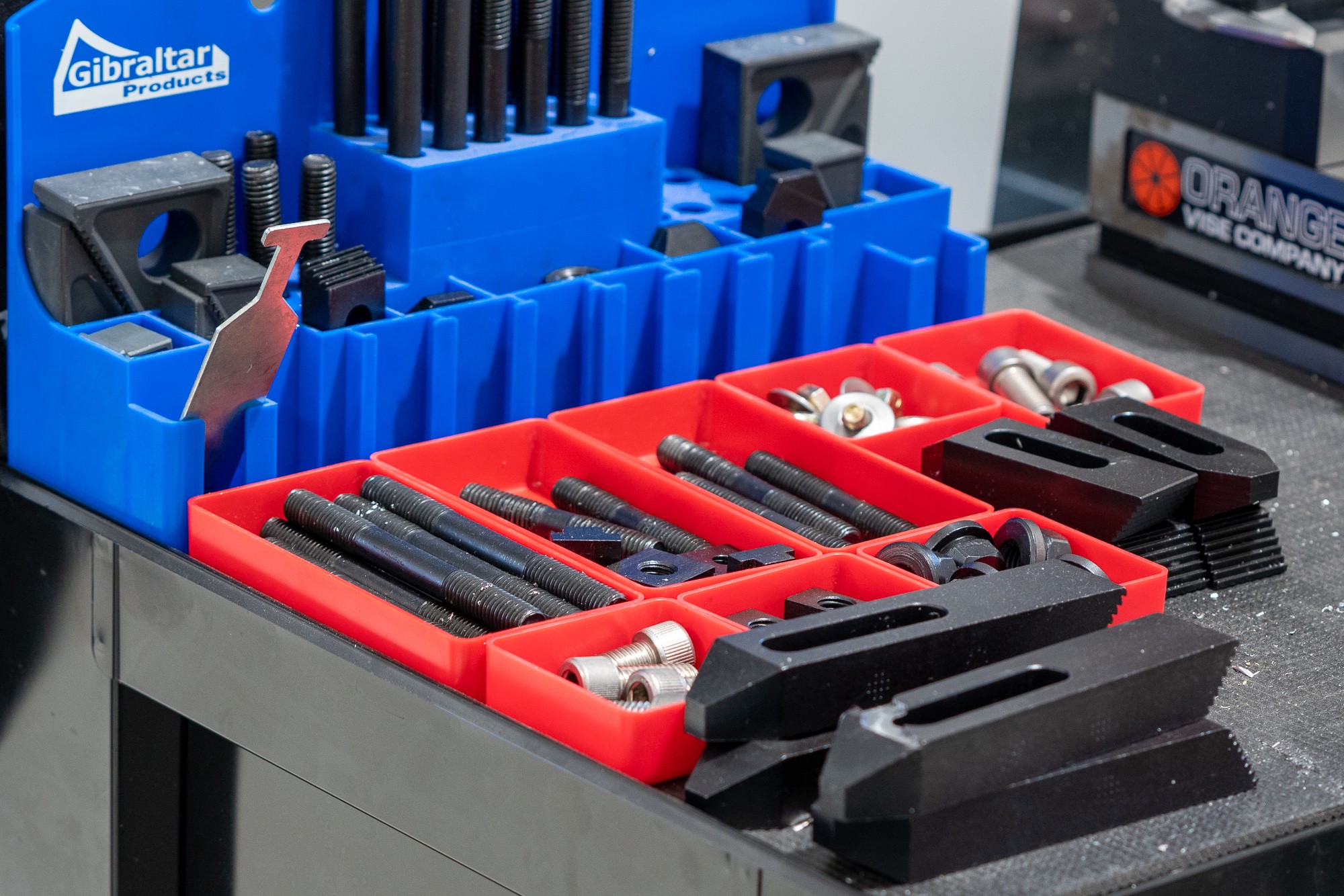
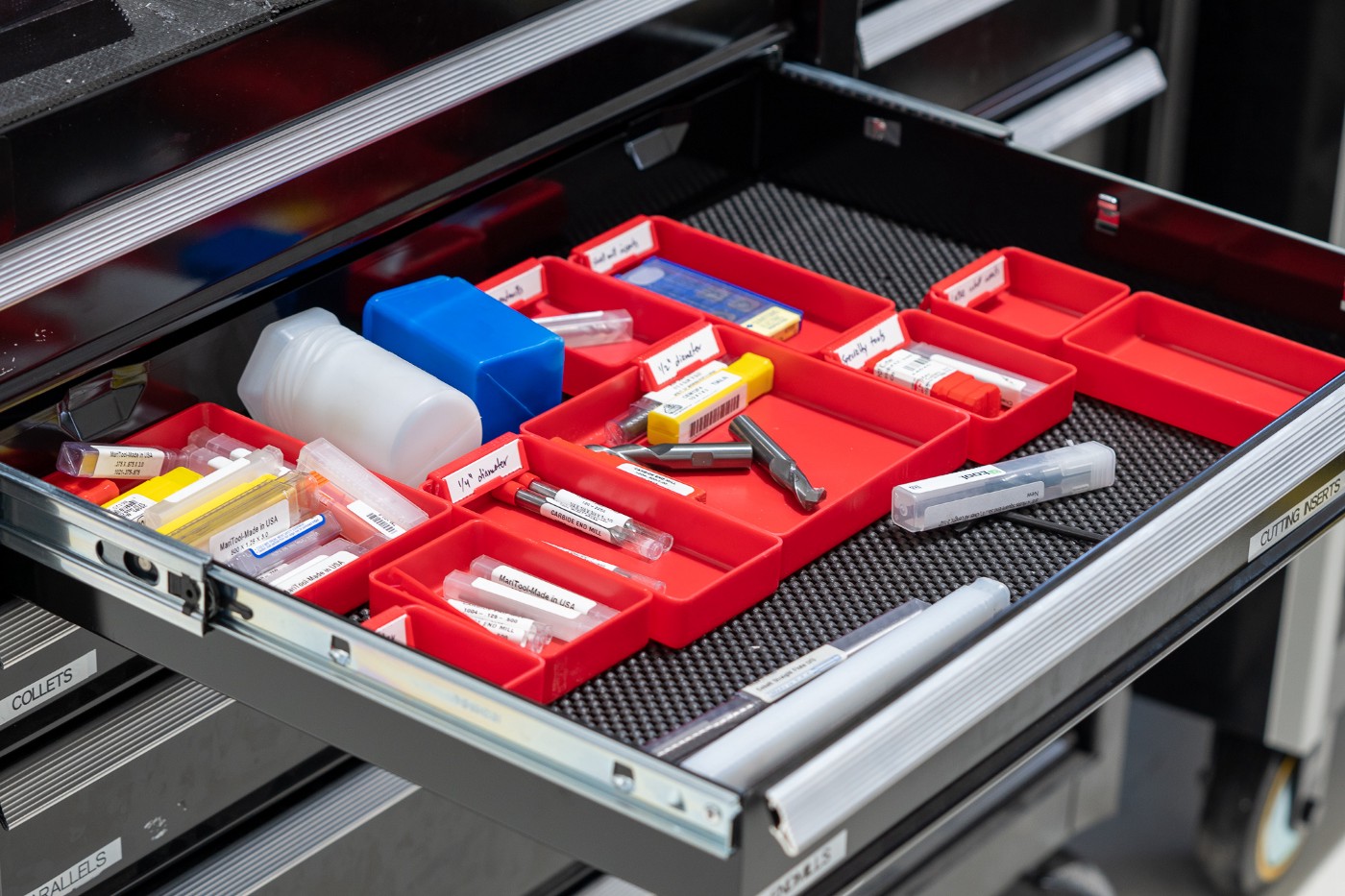
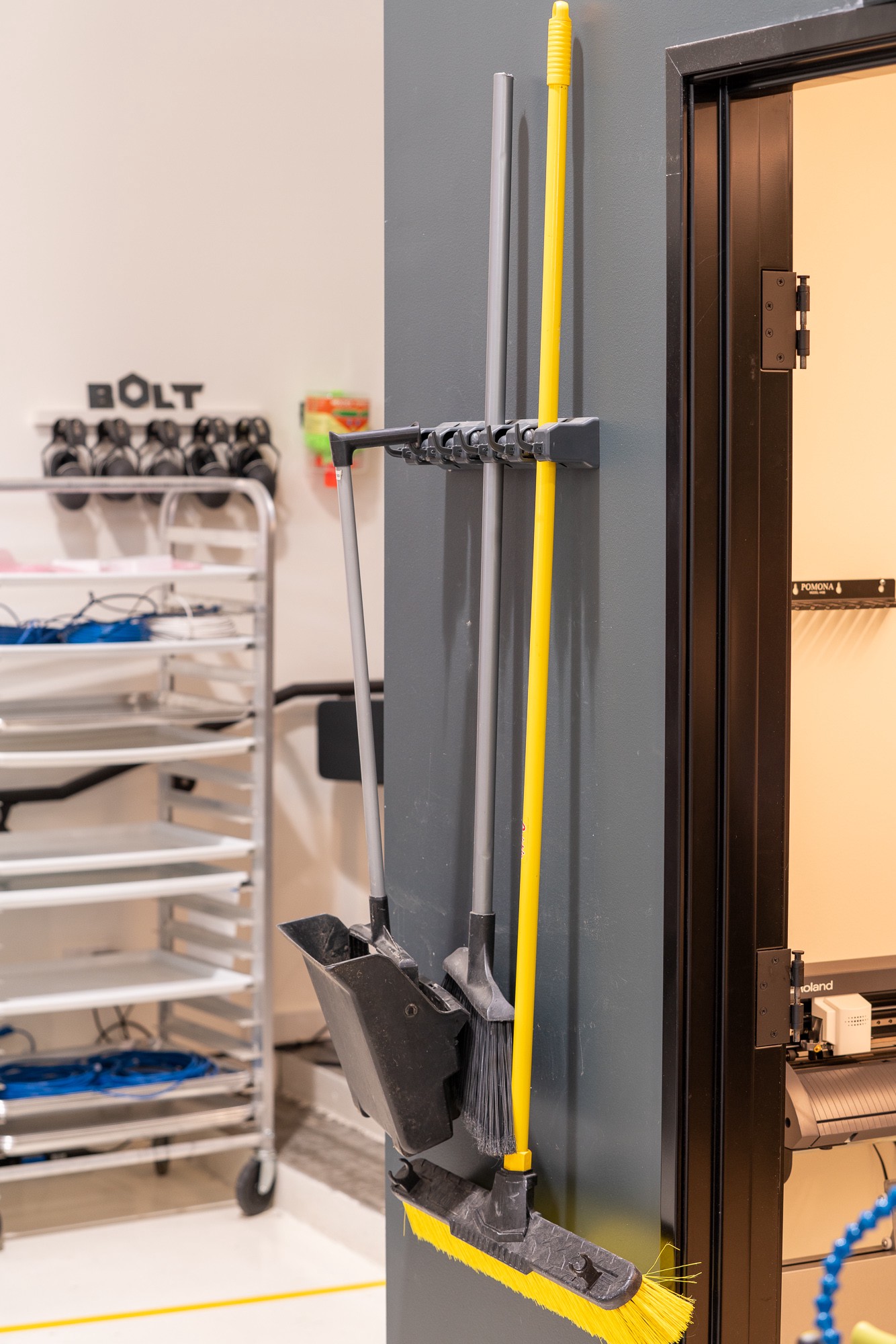
PPE (Personal Protective Equipment)
My theory on the most efficient way to keep shop users safe is to effectively make it impossible to avoid wearing PPE. How? Make it easy for users to find and grab whatever they need. Folks that work in the shop are always in a hurry, so if it’s too time-consuming to find some safety gear, they may skip it just that one time for that tiny little thing they need to do.
To start, safety glasses, ear muffs and plugs are mounted to the wall immediately as you enter the door. Check out these ear plug dispensers, which attach to the wall and are easy to replace when you run out; just pop the old case off and put a new one on the previously-attached mount.
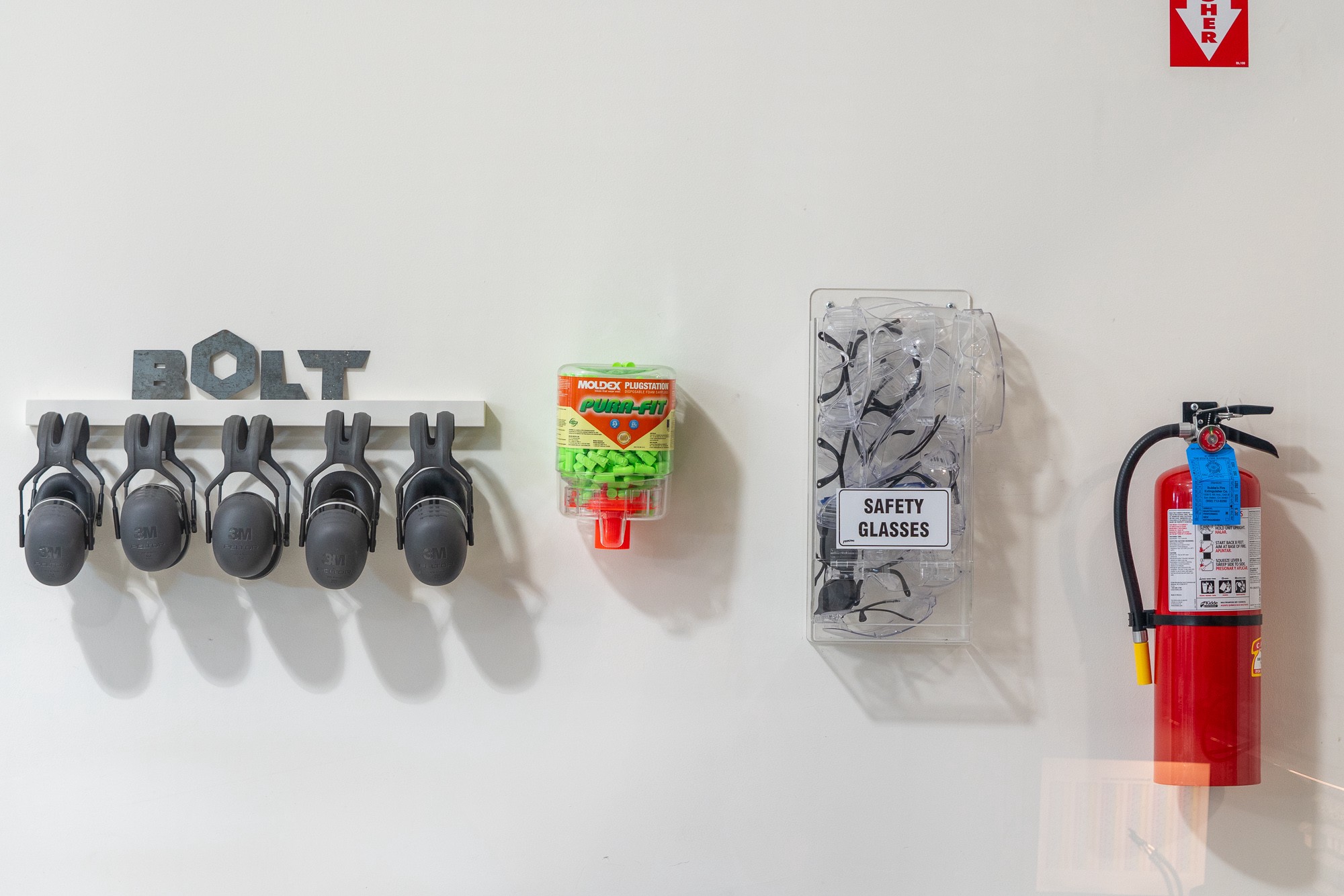
As a glasses-wearer myself, I know the pain of dealing with standard safety glasses. Frankly, the vast majority of them work terribly for glasses wearers, but these don’t. Pick up a few and keep them around; glasses-wearers will love you for it.
For tasks where full face protection is key, such as angle grinding or removing parts from a nasty chemical bath, keep some face shields on hand.
For removing parts from our base bath (which is used to dissolve support material from 3d-printed parts), we’ve had a lot of success with stainless steel hemostats and spider strainers.
Fume and dust extraction are key for maintaining good respiratory health. For our electronics lab, we invested in a nice fume extraction setup and recommend you do the same, whether it’s by placing a small extractor at each bench or purchasing a larger system that connects to multiple areas. We have the Dual 400 from Sentry Air Systems, which has plenty of power and an easy-to-replace filter, but the arms that came with it weren’t ideal. We swapped them out with some ducting and locline hose that’s easy to position at each soldering station.
Remind folks to shut off the extractor when not in use or you’ll blow through filters quickly.
If you do any woodworking, you’ll want a dedicated dust extractor to keep the airborne particles at bay. Don’t mix metal and wood shavings in a typical extractor, or you may get a boom. We have this one in our shop, which is connected to our chop saw, table saw and belt sander with some y-fittings and anti-static hose.
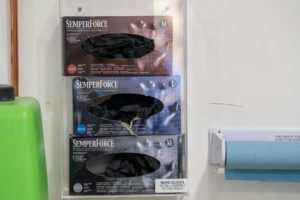
Based on the small amount of metal deburring and grinding we do, we haven’t found it necessary to invest in metal dust extraction. Thankfully, due to its mass, metal dust falls out of the air much faster than wood dust and is, therefore, less harmful to us.
Lastly, it’s great to keep gloves around in a few sizes. We keep ours mounted above the sink, near where they’re used most (the 3d printers and support material removal bath). Make sure to clearly mark where they’re not allowed, though: fast rotating tools.
Foster a community where users can share when something goes wrong
One of the easiest ways to improve safety in the shop doesn’t require purchases at all. Accept the fact that things happen to machines that causes them to misbehave and foster a community where users can comfortably share when something goes wrong. If users are afraid of the consequences that come with accidentally breaking something, they may not share that a machine is malfunctioning. This could lead to an unaware user attempting to use the broken machine, potentially injuring them.
While developing a hardware product as part of a fast-growing startup, the ability to iterate on your design quickly is key. By keeping our prototyping space well-marked, organized, and safe, our portfolio companies can work efficiently. If they can’t clearly mark something to recover later, find a tool they need or a piece of gear that will allow them to stay safe, we’ve slowed them down. And in the world of startups, that can be detrimental.
Bolt invests at the intersection of the digital and physical world.